Au programme: Analyse de 3 brevets portant sur la semelle de la future Ultra BOOST
Cet article ne présage pas des futures sorties de la marque, ce n’est pas un test de la chaussure, il n’est issu que de mon analyse de brevets déposés par la marque et reflète potentiellement les activités des concepteurs.
Les informations présentées dans cet article proviennent des brevets EP2767181, EP2649896 et US2014223777A1 déposés par Adidas AGeTPU
eTPU pour Expanded Thermoplastic PolyUrethane, c’est la base de la semelle Boost d’Adidas. Ce matériaux développé par BASF est la base de ces 3 brevets. Le brevet EP2649896 commence par une comparaison de l’eTPU et de l’EVA (Ethylene-Vinyl Acetate) souvent utilisé chez la concurrence (par exemple Asics).
Adidas met en avant 5 propriétés de ce matériaux face à l’EVA :
- La durabilité : après 100000 cycles de compression, l’eTPU se dégrade moins: 60% de compression en moins comparé à l’EVA, on obtient donc une semelle qui dure plus longtemps.
- Sa capacité à se comprimer : sur une même foulée, on obtient une compression de la semelle de l’ordre de 4mm avec l’eTPU contre seulement 1mm pour l’EVA. On a donc une chaussure très confortable à l’amorti
Comparaison de la compression entre l’EVA et l’eTPU sur une foulée - L’énergie perdue : on parle ici de l’énergie qui sert à comprimer le matériaux et qui n’est pas restitué au moment de l’expansion (par exemple par échauffement). Pour le coureur cela représente, l’énergie que l’on met à l’impact pour comprimer la semelle (et amortie le choc) et qui n’est pas restituée par la suite. On parle ici d’un gain de 25% avec l’eTPU
- L’indépendance thermique de la dureté : tout le monde a déjà constaté que les semelles EVA par grand froid, c’est un peu dur comme du béton alors qu’à 20°C c’est parfait ! L’eTPU est a quasiment une dureté constante quelque soit la température : on a donc des propriétés constantes!
- L’isolation thermique : 30% d’isolation thermique en plus comparé à l’EVA : on peut donc imaginer la semelle de propreté, qui sert aussi d’isolant, n’est plus de réel utilité ici.
De tout cela en résulte, l’atout clé d’Adidas : le confort ! C’est un point sur lequel les brevets insiste.
La conception des semelles
Le brevet EP2649896 définit les possibilités de conception offertes par l’eTPU.
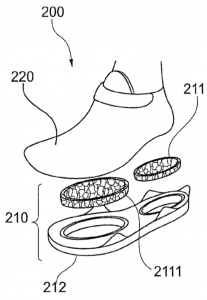
La première solution proposée est de mettre de l’eTPU là où il y a de l’impact : au niveau du talon pour amortir l’impact et offrir du confort mais aussi sur l’avant du pied, qui impact en dernier le sol (dans une attaque talon) l’eTPU apporte ici un rembourrage élastique qui permet de retransmettre une partie de l’énergie de l’impact au moment où le pied quitte le sol (zone 211). Le reste de la semelle : zone 212 peut être en EVA ou expanded PP, plus léger, un matériaux qui permet d’encaisser mieux les accélérations latéral ou les « déformations » de la foulée (pronation, supination..)
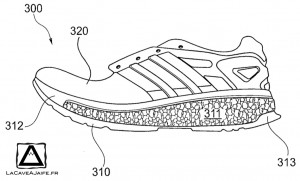
Le second arrangement consiste à mettre une zone sans eTPU exclusivement à l’avant du pied au niveau des orteils : un avant trop mou peut laisser une sensation déplaisante de glissement du pied dans la chaussure et être source de formation d’ampoule (dixit le brevet) d’où ce choix On reconnait ici le design de la semelle de l’adiZero Boston.
D’autres solutions sont développées dans ce brevet (semelle avec différents « grains » d’eTPU, différentes densités, des zones d’arrangement préférentielles de l’eTPU pour une meilleure isolation) mais je ne les développerais pas ici. Il est à noter que la semelle ainsi conçu est tellement confortable et isoler thermiquement qu’Adidas propose de réduire au minimum (voir de supprimer) la semelle de propreté.
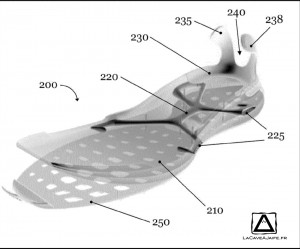
Le brevet EP2767181 amène une seconde particularité des semelles de la marque allemande : l’insertion d’élément dans la semelle. L’avantage d’utiliser un matériau tel que l’eTPU permet d’emprisonner dans la structure de la semelle des éléments de renfort et maintien sans utiliser d’adhésif. L’élément présenté sur la figue ci-contre par exemple permet d’accroire la stabilité et la capacité à se déformer de la semelle tout en permettant l’utilisation de matériau expansé.
![[Brevet] La semelle de l'Ultra BOOST par Adidas en 3 brevets 2](https://www.lacaveajaife.fr/wp-content/uploads/2015/02/Capture-d’écran-2015-02-02-à-22.07.23-244x300.jpg)
On pense ici au Torsion Bar de la marque : cet élément qui permet des mouvement de torsion indépendant de l’avant et de l’arrière de la chaussure.
L’autre élément de la marque qui peut être incorporé dans la semelle est le « heel clip » : une structure composée de 2 doigts avec un renfoncement au milieu. Elle a pour but de maintenir l’arrière du pied avec ces 2 doigts tout en évitant les frottement au niveau du talon d’Achille.
Une fois que l’on a une bonne semelle confortable, dernier élément qu’il faut traiter : la semelle extérieure. Elle l’est spécifiquement dans le brevet US2014223777. L’utilisation d’eTPU arrangé de façon aléatoire permet d’avoir une semelle légère qui absorbe bien les chocs mais il lui faut des éléments de contrôle pour transmettre au mieux les efforts !
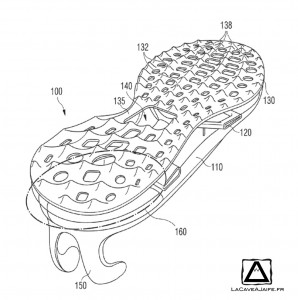
La semelle extérieure est constitué de protubérances (138), qui ont une plus grande raideur/fermeté que la semelle en eTPU et renfoncement (132). Après avoir touché le sol, les protubérances se déforment et viennent appuyer sur la semelle intermédiaire en eTPU pour transmettre les efforts et influencer les propriétés de flexion de celle-ci.
La semelle et particulièrement la zone autour du talon est soumise à une plus forte contrainte de cisaillement, quand le pied vient impacter le sol avec une attaque « talon ». Sur la zone avant du pied, un effet de soutien et de stabilité sont toutefois très recherché en fin de cycle quand le pied vient pousser le sol.
Le graphique ci-dessous montre qu’à l’impact la semelle en eTPU avec un rebord en EVA offre une plus grande déformation au cisaillement (2.4mm) qu’une semelle en EVA (0.6mm), ce qui implique une meilleur absorption du cisaillement entre la semelle extérieur et le haut de la semelle intermédiaire.
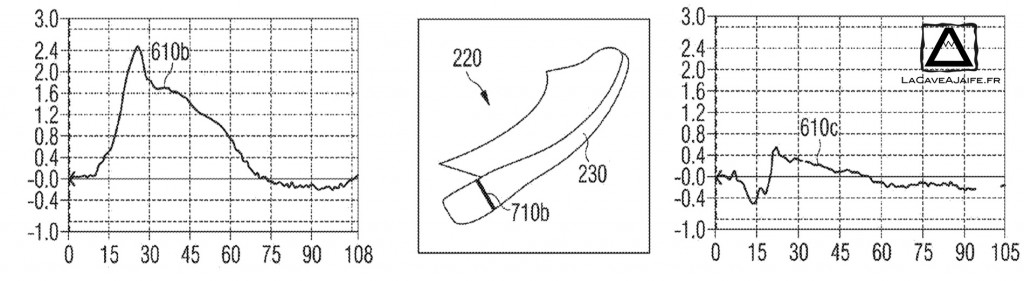
En appliquant tout cela, on obtient aussi une semelle plus stable à l’impact qui se déforme moins latéralement (0.5mm) que semelle en EVA (1.1mm). De même, à la relance, il n’y a pas de déformation latérale ce qui procure plus de stabilité et une meilleur dynamique.
La fabrication
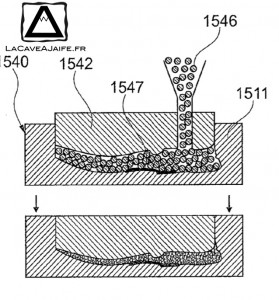
La création de la semelle se fait en 3 grandes étapes :
- Les milliers de billes d’eTPU qui sont de l’ordre de 3 à 8mm, sont d’abord chargées de façon aléatoire dans un moule. C’est un gros avantage : pas besoin de les aligner pour avoir les propriétés attendues !
- Le volume du moule est ensuite réduit jusqu’à la forme de la semelle définie ce qui a pour effet de comprimer l’eTPU. Cette effort induit directement sur la densité et la dureté de la semelle.
- Le moule est ensuite rempli de vapeur pour agglomérer les particules entre elles et former la semelle granulaire. Il est ensuite refroidi et enfin ouvert.
Pour les éléments supplémentaires, Torsion Bar ou heel clip, sont préférentiellement inclus dans la semelle intermédiaire en les entourant avec le matériau expansif. Cette méthode a l’avantage ne pas utiliser de colle. Une autre solution proposée est d’utiliser les propriétés chimiques des matériaux de la même famille (par exemple TPU et eTPU) pour créer une liaison solide entre les éléments sans utiliser de colle.
Le brevet indique que la semelle extérieure peut être découpée par laser via une ébauche comprenant les protubérances. Ce principe permet de fabriquer un grand nombre d’ébauche, et de venir découper les zones évidées en fonction de la chaussure finale : 1 ébauche, plusieurs modèles possibles! Ce type de découpage permet aussi une personnalisation de la chaussure mais ça ce n’est pas pour tout de suite pour le commun des mortels !
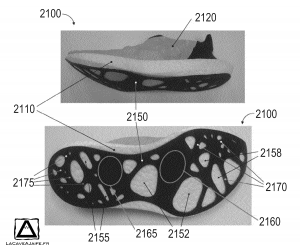
L’ultra Boost
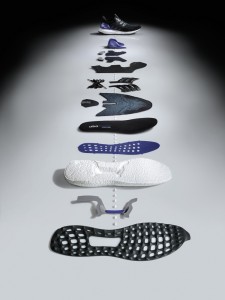
Ces 3 brevets mène à ce qu’Adidas à appeler la chaussure de running la plus aboutie jamais conçue : l’Ultra Boost. Mais l’utilisation de technologie a prix : 180€ !! En vente à partir du 11 février.
Tout y est : semelle avec 2 densités d’eTPU soit 3000 capsules en tout, semelle de propreté réduite au minimum, Torsion Bar et Heel clip sur la semelle intermédiaire et une semelle extérieure type « toile d’araignée »
On pourra toujours remettre en cause son gain sur l’efficacité de la foulée mais je pense que ce produit sera surement la chaussure la plus confortable de la marque allemande.
Il faudra attendre les tests qui devraient fleurir d’ici la fin février pour avoir plus de détails sur les ressentis, il sera, comme toujours, difficile de juger proprement le gain énergétique.
Je vous invite à regarder cette vidéo sur sa fabrication
Aux vues de ce qui est proposé dans les brevets, il y a encore des améliorations possibles pour la semelle de l’Ultra Boost, peut-être pour une version 2..
La technologie Boost a aussi récent été décliné sur la version outdoor des chaussures de la marque : la Terrex Boost
En attendant, si vous voulez un petit test des produits de la marque incorporant la semelle Boost, je vous invite à lire les différents articles de Daddy the Beat , Greg runner ou Jahom sur ces chaussures
Tout ce que j’en sais, c’est que je comprends rien à leurs 10.000 modèles, que c’est vachement cher et qu’ils me fatiguent avec leurs opérations de floodage des réseaux sociaux. Voilà ! #grincheuse
Mais j’apprécie le travail scientifique d’analyse des brevets by Jaife, ça change des discours commerciaux habituels 🙂
Merci Manue !
Quand je vois le nombre de test « vide » ou fait à la vite, je trouve qu’il est plus intéressant parfois de mettre en évidence le travail des ingénieurs plutôt que celui des marketeux
Je voudrais savoir a quoi servent les espèces de picots sur les côtés de la semelle des adidas traîner 3. Merci pour vos réponses